Vapor-X™ (ETI-900)
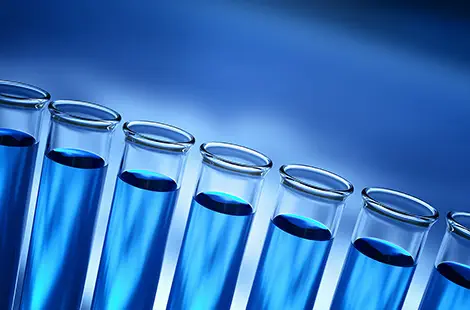
Vapor X™ (ETI-900) is a liquid product used to perform cleaning and/or decontamination in either liquid or vapor phase.
Vapor X™ (ETI-900) is used primarily for vapor phase or steam injected chemical cleaning and decontamination. The Vapor-X chemistry eliminates hydrogen sulfide gases, LEL, VOC’s and benzene. The Vapor-X process is safe, effective, and greatly reduces the volume of effluent normally required.
It contains a mild oxidizing agent. The mild oxidizing agent will oxidize and destroy H2S. The chemical mechanism of the reaction is quite complex, and several sulfur products are formed, including elemental sulfur (S°), sulfite (SO3=) and sulfate (SO4=). Significantly, these products are not toxic.
As an oxidizing agent, a second important function is the “taming” of pyrophoric iron sulfides that frequently exist in refinery vessels. Organic sulfides, commonly present as mercaptans, are ubiquitous in crude oils. When these sulfur-laden crudes are processed in a refinery, contact with iron alloys in refinery units inevitably leads to the formation of a whole host of iron sulfide compounds, including -- but not limited to -- pyrite, mackinawite and greigite. Normally, these iron sulfides do not present a problem during a refinery shutdown. However, if they have been formed in such a way that they are present as a very fine powder (particle size ~ 1µ), they will react with Oxygen as unit is opened for entry. The result is a fire!
Although the action of the oxidizing component in Vapor X™ (ETI-900) to “tame” pyrophoric iron sulfides is rather complex, there is a way to visualize it. During a decontamination operation prior to opening a unit for entry, the oxidant reacts right at the surfaces of solid iron sulfides. This reaction generates a film, a thin coating, of iron oxide (Fe2O3.xH2O) on those surfaces. Once that coating is formed, it provides a protective barrier against O2 contact with the underlying iron sulfide when the vessel is later opened for inspection and maintenance. This can be thought of in much the way we think of a coating of paint on wood to protect the underlying wood from decay. Thus, Vapor X™ (ETI-900) is capable of deactivating (“taming”) pyrophoric iron sulfides during a job without the necessity for complete removal or chemical destruction of all iron sulfides within.
Vapor-X™ causes little change to operations original shutdown procedure and greatly reduces the period of time required for conventional steam out and subsequent maintenance activities. Vapor-X™ has very low COD (chemical oxygen demand), and can be used in a multitude of applications, especially where liquid-filling is not an option.