High Sulfide Deposits from Process Equipment
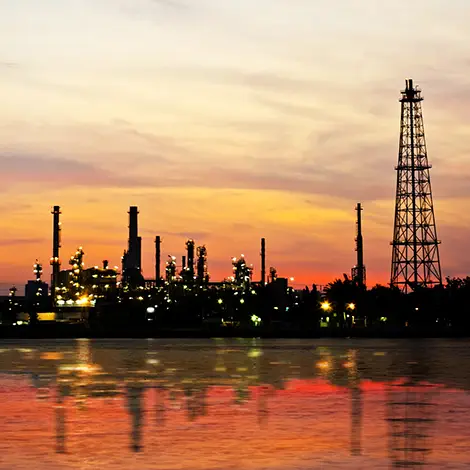
Case Study:
High Sulfide Deposits from Process Equipment
EnvTech Inc. was awarded a chemical cleaning contract for a Northern California, refinery wide shutdown. The shutdown involved the hydrogen, hydrocracker, sulfur gas, FCC, utilities and pipestills units. In the past, standard cleaning methods for the removal of hydrocarbon and sulfide contamination from process equipment involved the use of a two-phase cleaning procedure (alkaline detergent phase followed by an acid phase, which required an additional step for neutralization). However, EnvTech developed an innovative, single phase decontamination process that was applied throughout the turnaround on more than 40 systems.
EnvTech eliminated the use of corrosive products and simplified the cleaning to one phase using two EnvTech products designed for refinery degassing and sulfide removal. The turnaround involved a wide variety of process equipment, including towers, drums, exchangers, piping systems and even a storage vessel that contained a 100% mercaptan, odorant product.
EnvTech Inc as a leader and innovator in process equipment decontamination has developed specific procedures and chemistries for each project, including coker fractionators, atmospheric columns, vacuum columns, and desalters.
EnvTech is able to provide cleaning and decontamination of each circuit in under 24 hours.
- Often, EnvTech results exceeded plant expectations to the point that much of the planned hydro-blasting work is no longer necessary.
Always, the process 100% eliminates pyrophoric material, including in packed column sections.
- On all EnvTech projects, exceptional results are achieved while complying with health, safety, and environmental requirements.
- The amount of effluent is always procedurally minimized, and the waste effluent is easily managed by the wastewater plant or treated onsite for immediate disposal.
The new procedures allowed refinery personnel and contractors to safely enter these vessels in record time to perform the necessary inspections and repairs.
Several of the Benefits Included
- A buffered 8.8 pH solution was used rather than corrosive products such as caustic or hydrochloric acid, thus avoiding unnecessary risks to personnel and equipment.
- The sulfides were oxidized during the degassing phase by the combined use of a newly developed ETI product providing the oxidation equivalent of hydrogen peroxide without the associated hazards.
- The extreme hazards that result from the liberation of H2S, when an acid is utilized, were totally eliminated.
The spent cleaning solution was environmentally friendly and the refinery’s waste water system was able to handle it at a substantially accelerated drain rate as compared to previously utilized chemistry. In addition, due to the single-phase method, less than half the quantity of previously used cleaning solution was generated.
- The cost of the turnaround diminished thanks to reduced cleaning time, reduced waste water generation, and reduced or eliminated need for follow-up cleaning by mechanical means.
- The non-corrosive cleaning method increased the life of the process equipment.
References available upon request.
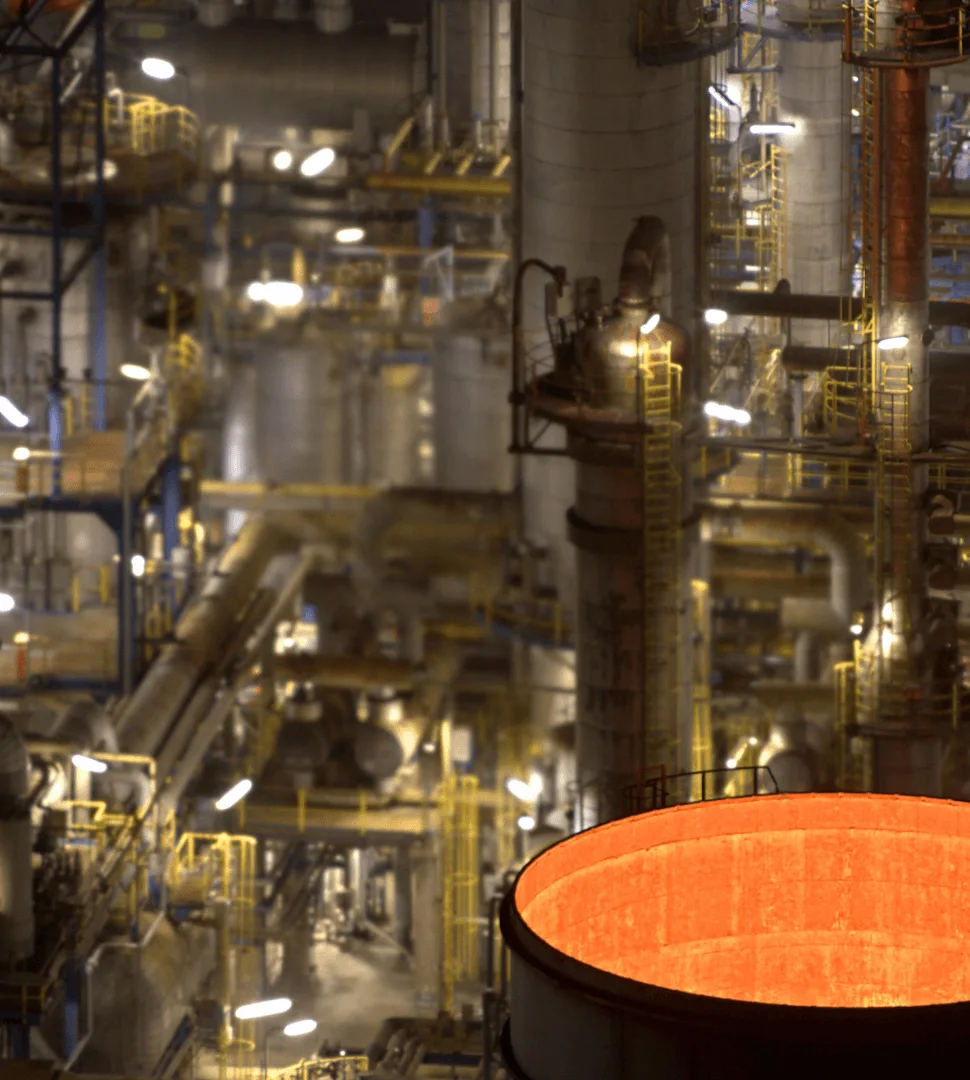