Decontamination of HF Alkylation Units
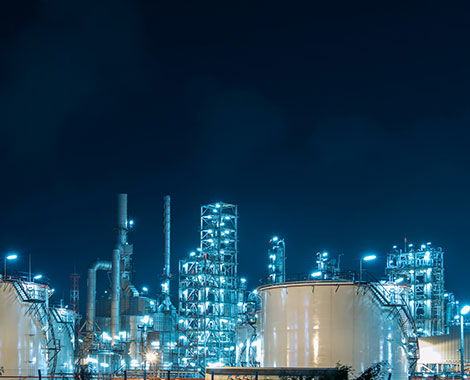
Case Study:
Decontamination of HF Alkylation Units
EnvTech Inc. has developed a state-of-the-art cleaning process for the decontmaination HF Alkylation Units. Most chemical cleaning contractors rely on a three-phase procedure using an acid for scale removal. Some utilize an ammoniated citric process that has a low pH step as the initial phase. The best way to demonstrate the advantages of EnvTech’s single phase cleaning and neutralization process is by comparing it with these alternative techniques.
Inhibited HCL, Sulfuric Acid and Ammoniated Citrate:
The problems associated with these processes include:
Corrosion inhibitors are inhibitors not preventers. Inhibitors slow down the corrosion rate of hydrochloric acid on carbon steel, but high temperatures, high liquid velocities, high iron levels and particularly HF concentrations above 0.25% compromise the inhibition performance. EPRI (Electric Power Research Institute) developed guidelines for the boiler industry regarding the use of HF for silica removal. They determined that the maximum level of HF present in the cleaning solution should be 0.25%. The HF is not inhibited nearly as effectively as the HCl. Temperature becomes a factor since polymer removal does not effectively occur at temperatures below 180º F while inhibition benefits begin to diminish above 140º F.
Exposure to the problems associated with hot acid solutions, particularly those containing levels of HF is unnecessary because EnvTech has developed a widely tested and proven pH-Neutral method.
Acid cleanings require that both phases (acid phase and neutralization phase) be rinsed thoroughly. This results in more than doubling the amount of downtime necessary to effectively clean & neutralize a system.
Acid cleanings generate more than twice the volume of waste water and the acid phase needs to be neutralized once it has been drained from the system.
Even after the system has been cleaned the complex nature of piping systems containing numerous “dead legs” invariably traps acid solution containing some level of un-neutralized HF in the system.
The use of ammonia creates unnecessary personnel risks as well as significant challenges for the refinery’s waste water system.
The Benefits of ETI Cleaning & Gas Freeing Solution:
- EnvTech’s proprietary “Clean &Gas-Free” process utilizes a strong 8.8 pH buffer. As a result, neutralization is affected immediately upon contact during the initial phase of the cleaning. In addition, “dead legs” filled with acid are avoided since the solution that fills them is buffered. Corrosion is eliminated because the water that is introduced to the system is buffered. Personnel are not exposed to the risks associated with circulation of hot acid solutions containing levels of HF.
- EnvTech’s proprietary chelant is utilized to create a “single phase” removal of Iron Fluoride deposits in combination with the neutralization chemistry. This mixture has proven excellent for polymer removal and can be heated to as much as 225º F without adverse effects.
- The EnvTech chemistry can, in most locations, be drained directly to the refinery’s waste water system. Where fluoride levels present a concern, EnvTech has developed a procedure for reducing the concentration to below 50 ppm.
- This single-phase method reduces the duration of the cleaning and neutralization of an entire Alkylation unit to under 48 hours. This single benefit often encourages many turnaround management teams to utilize the EnvTech Difference.
- EnvTech has demonstrated the effectiveness and reliability of this process throughout the world. Due to the number of HF projects performed, the skill level and experience of ETI personnel is unmatched.
EnvTech engineers work closely with the refinery’s HF Alky team to develop a detailed procedure that ensures the entire system is neutralized in order to avoid leaving any pockets of HF for mechanical teams to discover. In addition, EnvTech is able to offer many cost cutting suggestions. Good planning and detailed discussions involving the EnvTech engineering team early on, create an excellent synergy and worthwhile results.
References available upon request.